|
SOLID CARBIDE ENDMILLS |
|
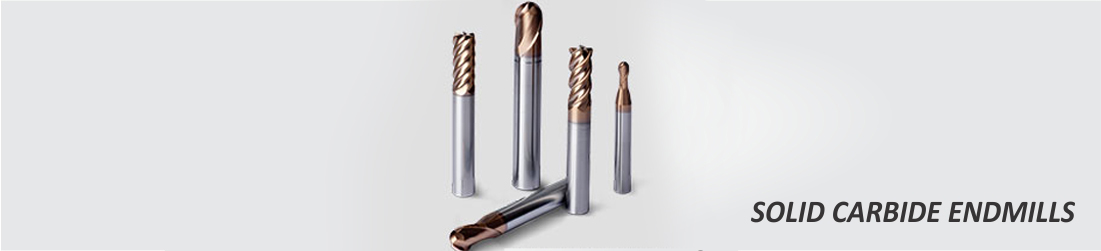 |
|
|
|
DIE AND MOLD ENDMILLS |
 |
|
Our range of Solid Endmills for die & mold come with a variety of series. Each series with their own characteristics and application strengths.
EP50
Our primary series made from sub micron carbide grades for machining of steels and cast irons up to 35HRC hardness. It is available in a variety of flutes, shank lengths and flute lengths to cater to the basic needs of the Die & mold plus the manufacturing industry.
SH160
The SH160 range is mainly to cater to the high hardness material machining requirements of the Die & mold industry. The carbide substrate & cutting geometries are designed in a fashion to optimize cutting forces and edge strength. The result, a thorough tool which is very keen solving your hardened Die machining. The SH160 is sufficient to machine material up to 55HRC in hardness.
|
|
|
|
|
ENDMILLS FOR STAINLESS STEEL |
Ss200 end mills are made from fine sub micron carbide substrate with high adhesion and wear resistance. Suitable for the heavy cutting as well as medium machining of stainless steels . With advanced geometries like variable helix and differential flute pitch, they are among the best solutions for machining of stainless steels in the cutting tools industry today. |
|
 |
|
|
|
|
|
|
ENDMILLS FOR NON-FERROUS MATERIALS |
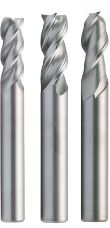 |
|
The UA100 series is designed with complex edge geometries for the reduction or complete elimination of vibrations in the machining process. The tough matrix material grade makes it suitable for the machining of aluminum alloys (Si < 12%) and copper alloys (<200HB). The carbide substrate come with high heat tolerance making water coolant the best cooling method.
|
|
|
ENDMILLS FOR SUPER HARD MATERIALS (UPTO 63 HRC) |
The SH200-H series is made from sub micron carbide substrate with high strength and high toughness material matrix with advance coating. The new AlTiCrSiN coating has high micro hardness couples with high oxidation hardness. These features make it ideal for the machining of very hard materials up to 60HRC. It was designed keeping in mind the high finishing requirements for hardened Dies, molds & components. |
|
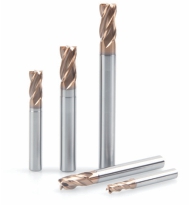 |
|
|
|
|
|
|
|